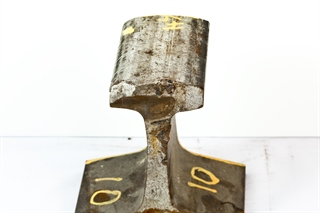
Rail integrity is critical to the railroad industry, especially since rail flaws and defects can lead to broken rails or even derailments. Because of the serious nature of rail flaws and their impact on safety, the industry has responded with improved rail maintenance practices and flaw detection methods.
One of the most important practices is the usage of non-destructive testing (NDT) methods. The included technology and testing methods must be capable of performing accurate, reliable, and effective tests in a constantly changing environment. In addition, testing must be at an acceptable speed that will not interfere with the service functionality of the railroad.
Current Technology
The ultrasonic non-destructive testing method is the most frequently used in the industry. Ultrasound uses sound waves, or vibrations, that propagate at frequencies that are above the range of human hearing (normally above 20,000 Hz or cycles per second). Ultrasonic waves are transmitted into the rail at various angles - from the top of the rail head through the web to the bottom of the rail and the entire width of the rail head - by piezoelectric transducers. If a flaw condition (rail head surface conditions, internal or visible rail flaws, or weld upsets or finishes) is encountered of sufficient size and orientation, the ultrasound signal is reflected back to the appropriate transducer. The information is then processed by the test system and recorded in the permanent test data record.
Detection Methods
Current detection methods use various types of mechanical processes that then require human involvement for the interpretation of the test data. The majority of testing is performed in a dynamic mode at speeds that work best with the railroad's system capability. The main four rail flaw detection methods used in the US include:

Portable test process: This method consists of an operator pushing a mobile test device either over one rail individually or both rails simultaneously (at a walking pace) while visually interpreting test data on a monitor. When a potential flaw is identified, the operator will stop and manually verify the location to determine if a flaw exists. The defect is then sized and the location within the rail section is identified. The operator will provide this information to the railroad for remedial action. In some cases, the portable test unit is able to provide a permanent digital test record for future analysis.
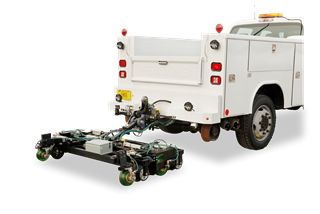
Start/stop process: This method consists of a vehicle-based (hi-rail or rail-bound) test equipment that is driven slowly over rail (usually not over 25 mph) while presenting data via a monitor to the operator for interpretation. When a potential flaw is identified, the vehicle is stopped and the operator will manually verify the location to determine if a flaw exists. The defect is then sized and the location within the rail section is identified. The operator will provide this information to the railroad for remedial action. This type of test method provides a permanent digital test record for future analysis.
Chase car process: This method consists of a lead test vehicle that performs the flaw detection process, followed by a verification chase car. When the lead test vehicle encounters a potential flaw, a copy of the location is electronically transmitted to the chase car. The chase car operator is then responsible for verifying if a defect exists and reporting any positive findings to the railroad for remedial action. This method allows the lead test vehicle to continue testing uninterrupted. This type of test method provides a permanent digital test record for future analysis.
Continuous test process: This method consists of operating a high-speed, vehicle-based system nonstop along a designated route; this allows testing of sections that exceed more than 100 miles per shift. The test data is sent to and analyzed at a designated remote location. Once the data is analyzed and it is determined that a section may contain a potential flaw, a report is sent to the verification staff. The verification operator will then confirm the flaw using a portable test unit or hand-held flaw detector. The verification report is then provided to the railroad for remedial action. This type of test method provides a permanent digital test record for future analysis.